Next-Gen Manufacturing: Achieving Success through Data-Driven Supply Chain Strategies
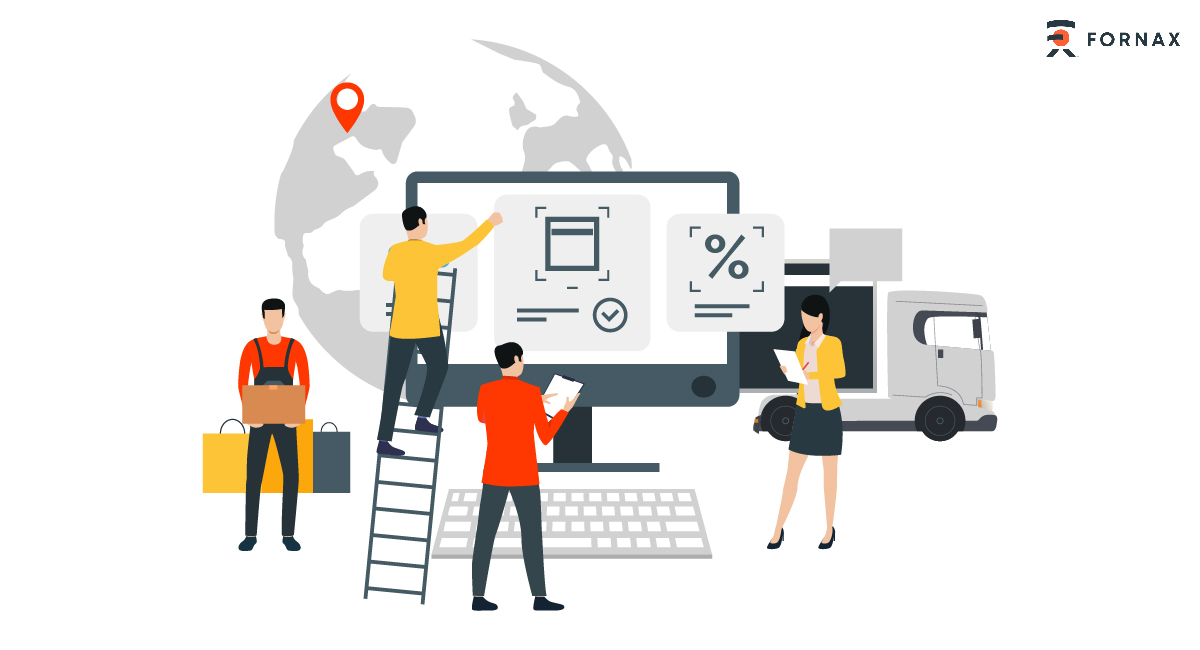
The manufacturing sector is undergoing a transformation powered by data, with cutting-edge technologies like industrial IoT leading the charge. Installing remote sensors on industrial equipment, warehouse assets, and even factory workers can gather, analyse, and leverage production data to boost productivity, profitability, and safety. Let's examine how data revolutionise manufacturing operations and some examples of manufacturing data in action.
Do you recall the first time you saw high-definition television? The more vibrant the colours, the greater the complexity and contrast of the images. Manufacturing is experiencing its own 4K moment, propelled by the ability to gather better and analyze the petabytes of data generated daily in a modern industrial setting.
Data quality is crucial for improving one's comprehension of the manufacturing process.
What is data warehousing?
Data warehousing is collecting, storing, and managing large amounts of data from multiple sources in a centralized repository. Data warehousing aims to provide easy access to the data, making it easier to analyze and use for decision-making purposes.
For manufacturing companies, data warehousing can be particularly useful in streamlining the supply chain. By collecting data from various sources, such as suppliers, distributors, and customers, manufacturing companies can get a better understanding of the supply chain and identify potential issues that could cause delays or disruptions.
The value of data for manufacturing
Smart manufacturing is now transforming practically every part of the manufacturing process, and it is progressing every day. Access to raw materials, affordable energy costs, and a diverse range of suppliers are essential for manufacturers. However, during economic uncertainty, they become especially vulnerable to disruptions. A single delay in their supply chain can have cascading effects across their entire value chain.
For instance, automotive OEMs depend heavily on partnerships and dealers, and customers often have no alternative but to wait out delays as parts are usually made to order.
Unfortunately, most manufacturers' systems need to be integrated, with their supply chain management operating independently from their enterprise resource planning software and back-office operations, as well as customer communication solutions. This limits their ability to make quick decisions to mitigate the adverse effects of disruption.
This disconnection can result in various problems. With an integrated data pipeline and visibility across their operations, a supply chain issue or delay may be effectively communicated to customers, making it easier for them to make contingency plans. Manufacturers, therefore, require suitable infrastructure and software to be adaptable, offer better services, and avoid such scenarios.
Here are some of the ways data is valuable for manufacturing:
Know about the current product preferences of consumers
Manufacturers can get information about how users in various markets engage with their goods and the value they place on existing and future functionality by collecting data from various sources. This understanding allows for reducing much of the risk associated with developing new products or redesigning old ones.
More precise forecasting of future demand
Manufacturers are confronted with a Goldilocks dilemma: how to manufacture just the right amount of product to meet current consumer demand? Too little causes shortages, whereas too much cause unwarranted price reductions. Data can be used to track previous demand, developing consumer patterns, weather occurrences, and other factors to assist producers in aligning production schedules with demand.
Improve output/throughput
Data from a network of sensors put on machines, warehouses, and intellectual capital can assist decision-makers in identifying possibilities to increase production. Manufacturers can increase profitability by recognising which aspects of the manufacturing process can be optimised using data analysis and modelling.
Quality control
Quality control difficulties lead to dissatisfied customers and reduced profitability. Warranty claims and production line data can be analysed by manufacturers to uncover trends that indicate a specific design flaw or manufacturing issue.
Increase worker safety
Front-line production, warehousing, and transportation personnel can benefit from manufacturing analytics. Wearable sensors can monitor the temperature, pollution levels, noise levels, and other stresses that employees are exposed to regularly, informing supervisors of the need for assistance. When a worker's stance deviates from expected norms, IoT sensors can notice an issue, such as falling or not adhering to suitable ergonomic placement.
The supply chain
Maintaining weak supply chains has grown into an increasingly challenging task. Yet, predictive analytics algorithms can warn producers of anticipated problems before they occur. Analytics systems can precisely foresee delays caused by weather, political upheaval, vendor insolvency, or transportation constraints using data from transport partners and third-party sources.
How is Data Reshaping Manufacturing's Supply Chain?
In a recent poll of over 1,000 executives by Oxford Economics, more than three-quarters of business leaders reported implementing AI in pilot programmes, important business sectors, or at full scale across the firm. The top challenge these installations are meant to address is cybersecurity, with supply chain management coming in a close second. However, the major hurdle to increased acceptance is the technology's sheer complexity, which must be deployed across various processes and infrastructures to generate the maximum advantage.
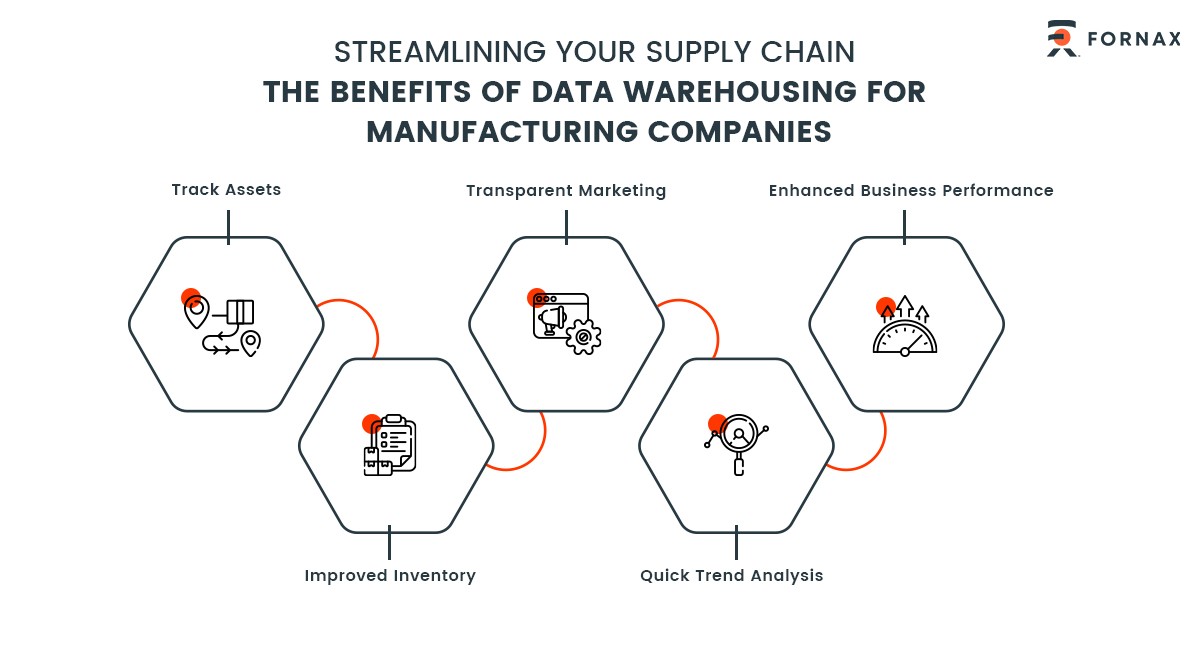
Improved Inventory
One of the key benefits of data warehousing for manufacturing companies is improved inventory management. By collecting and analyzing data on inventory levels, manufacturing companies can better anticipate demand and adjust production accordingly. This can minimize excess inventory, reduce storage costs, and improve cash flow.
Track Assets
Manufacturing companies often rely on a network of suppliers to provide the raw materials and components needed for production. With data warehousing, manufacturers can collect and analyze data on supplier performance, such as delivery times and quality of goods, to identify any issues that could be causing delays or disruptions in the supply chain. By addressing these issues, manufacturers can improve their relationships with suppliers and ensure a more reliable supply of materials.
Transparent Marketing
Data warehousing can also help manufacturing companies optimize their production planning. By collecting and analyzing data on production times, equipment utilization, and other factors, manufacturers can identify bottlenecks in the production process and make adjustments to improve efficiency. This can help to reduce production times, improve quality, and increase throughput.
Quick Trend Analysis
Manufacturing companies that rely on a complex supply chain to deliver their products to customers can benefit from data warehousing by improving customer service. By collecting and analyzing data on customer demand, order history, and delivery times, manufacturers can better anticipate customer needs and ensure the timely delivery of products. This can help to improve customer satisfaction and loyalty, leading to increased sales and revenue.
Reduced costs and Enhanced Performance
Finally, data warehousing can help manufacturing companies reduce costs throughout the supply chain. By identifying inefficiencies and bottlenecks, manufacturers can make adjustments to improve efficiency and reduce waste. This can lower production costs, reduce storage costs, and improve cash flow.
Bottom Line
The correct software will assist you in streamlining your supply chain processes. A proper ERP solution may improve your supply chain procedures, from asset and inventory management to generating educated decisions. It's critical to make informed inventory decisions, and your plan wants to know its status in real-time. Conversion from sales to inventory management can improve the overall efficiency of the supply chain process at all company levels.
Get in touch with our experts today!